Docks
Dock Construction/Repair Considerations (June 2021)
For those of us that live on a lake, one of our major investments/assets is our boat dock. This article may be helpful to add life and reduce overall cost to maintain it. We hope if nothing else we encourage you to check out the issues and enjoy the long use of this asset.
Joists
While we spend a lot of time during thinking about the surface we walk on, there are other critical components to consider. Joist support members in many cases will not last as long as the vertical support posts or the decking. If the deck is constructed from Composite Materials like Trex or exotic hardwoods like Ipe, Cumaru, Tigerwood and so on the materials will most likely last years longer than the joists if maintained properly.
Joist material should be Marine Grade Treated Wood material for docks. Most of the treated lumber you can buy at Lowes or Home Depot is not the higher quality material needed and will deteriorate faster. There are a couple key things to consider.
- If your deck material is an exotic hardwood, it should be treated annually with an oil. These wood types are loaded with oil and very dense. DO NOT PAINT IT. Paint and or Water repellent products do not soak into the wood and can speed up deterioration. There are some very good products for this like Penofin & Ipe Oil for example.
- When your joists are installed by your contractors watch out for these two areas.
- A common practice/habit the contractors use is to drive larger diameter nails in about ¼” to space out the deck planks. They remove them when the deck is fastened. While the treatment process does help with rot it does not protect against moisture getting into the wood fibers and this practice opens the pores at the top of the joists and many times accelerates the moisture penetration from the top and breaks the wood down prematurely.
- Lack of Joist protection. Joist tape is an affordable way to protect your deck substructure. Peel-and-stick flashing tape allows the wood to breathe because it is applied as a cap directly on top of joists and beams. The tape protects screw holes from moisture by acting as a barrier. This tape lasts for as long as the deck and is less than $200 for most docks. It’s a very small price to pay to ensure that your entire system has similar life expectancy. Some choices are Trex Protect, Deckwise, & Grace Vycor.
Structural Materials
For structural materials here are some things to consider. Choose the right treatment level depending on the kind of water you are building in:
Fresh water: A minimum of .60 pcf pressure treated wood.
Saltwater: 2.5 pcf pressured treated wood (or higher) is required
For decks and docks of all kinds, many contractors choose UC4B and UC4C for the decking and framing. Experienced contractors know that you need to have lumber that is certified for “ground contact” or higher for humid, harsh, or near water applications.
These treatments help protect lumber from rot, moisture, and burrowing pests—and to prevent the treatment in your lumber from seeping out into the environment. This lumber can often be used in environments where occasional saltwater contact is likely, such as framing over saltwater. Lumber that is not safe for ground contact will wear away faster and may even cause damage to the flora and fauna surrounding it.
If you are looking for lumber to use in an ocean environment, look for wood that is labeled as “marine grade” or classified as UC5B and UC5C. This indicates that the wood can withstand continuous saltwater exposure. Salty or brackish water is more abrasive than freshwater, so using ground contact-certified lumber is not enough for these settings.
Another important acronym to pay attention to on a lumber label is the type of preservative that was used to treat the wood.
To prepare it for harsh marine environments, wood is pressure treated with a combination of water and preservatives to keep pests away and slow the rate of decay. Different preservatives are suited for different applications and types of wood. Let’s go over some of the most common treatments you’ll see in marine lumber.
- MCA (micronized copper azole) and CA (copper azole) – Copper-based preservatives suitable for above-ground, below-ground, and freshwater uses. These treatments penetrate deep into lumber to prevent rot from water exposure and pests.
- ACQ (alkaline copper quaternary) – Contains a quaternary compound including copper and ammonium. ACQ is strong against fungi, insects, and other marine creatures that may damage the integrity of lumber.
- CCA (chromated copper arsenate) – A combination of chromium, copper, and arsenic for maximum protection. Because of its chemical content, CCA is approved for marine construction but not for most residential applications (like in homes, fences, or furniture). Source: US Forest Products Laboratory
All of these treatments are water-based (as opposed to oil-based). That allows the treatment to fully penetrate lumber while still allowing the application of paint and finish.
Because of the power of each treatment type, you’ll need hardware that won’t rust or wear down the wood. Be careful with some materials like hot dipped galvanized fasteners because some of the treatments used cause them to rust/corrode quickly. Stainless and Coated Fasteners are best.
Breaking Down the Lumber Label
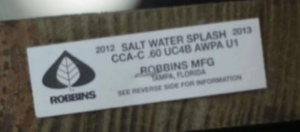
Now that you have a better understanding of the different acronyms used to describe lumber labels, let’s break down the label above.
-
- CCA-C is the active ingredient—in this case, chromated copper arsenate, type C.
-
- 0.60 is the lumber’s retention rate, or the amount of preservative used to treat the wood. The higher the retention rate, the lower the biodeterioration rate.
- UC4B is the Use Category. UC4B lumber is suitable for ground contact and contact with freshwater. It is also durable enough to be used for “critical construction” projects, such as utility poles.
- AWPA U1 signifies that the wood has been treated according to AWPA Standards.
Boat Dock/Deck Materials Pros and Cons
For the decking materials here are some things to consider. If you are looking to build or rebuild a boat dock you want the most durable wood that will last a lifetime with very little maintenance. A boat dock sees some incredibly harsh conditions since they are so close to the water, they are typically getting abuse from waves and are often constantly saturated with water. Constant moisture is an enemy for all boat dock materials whether they are wood or composite. In fact, constant moisture can lead to faster rot and decay, mold and mildew and leave you with excessive maintenance.
Pressure Treated Pine
Pressure treated pine is the most common and affordable type of wood commonly used for boat docks. The pros of using this material is the initial cost is the cheapest compared to other options. This material is supposed to last you 20 years or more with annual maintenance but here in Florida it rarely does. The cons are the annual maintenance that will be required. A Pressure treated pine boat dock will need to be sealed every year or every other year with a water sealer to keep the water from saturating the wood. If this is not done it will lead to early rot and decay of your boat dock since pine is a soft wood. Soft woods are more prone to rot and decay, insect attack as well as mold, algae and fungi growth.
The regular maintenance costs will add up over the lifetime of your dock so make sure you plan for the square footage of you boat dock and how much water sealer you would need as well as the other materials needed (pressure washer, brushes and etc…) Pressure treated pine is also known to splinter overtime which can be bad for a boat dock if you are using your dock with bare feet. Many boat docks also serve as a swim platform with a ladder built on.
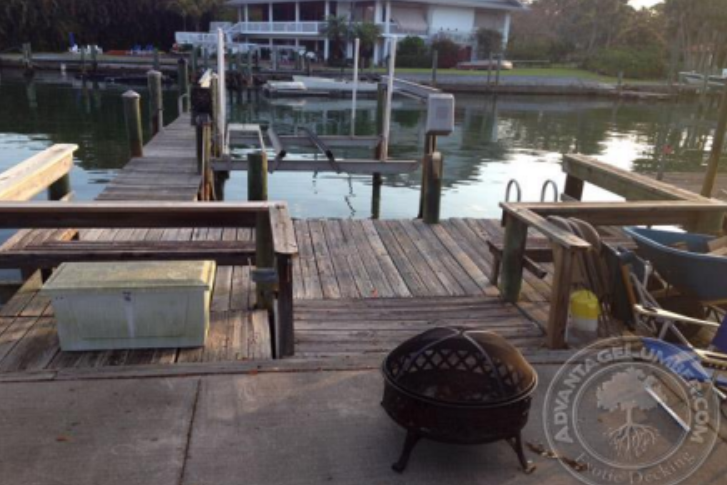
The pressure treated pine boat dock above has weathered severely. Additionally, the wood has splinters all over and is rotted in parts that had seen more water.
Cedar Wood
Another softwood option is Cedar which is considered an upgrade compared to treated pine. Although Cedar is known to have some natural rot resistance but it still requires a water sealer applied every year or every other year to keep the water from rotting the wood.
In the picture above you can see it still splinters and will rot which is why the deck board above is being replaced. The waterproofing sealer will eventually flake off as seen in this photo.
Pros:
- 25+ year lifespan
- Can be stained
- Some natural rot resistance
- Not hot on bare feet
Cons:
- Requires annual maintenance with a waterproofing sealer that will eventually peal off.
- Contains knots.
- Splinters will eventually occur.
- Will eventually rot.
Composite Dock Materials
Composite deck and dock materials have built a notion that it is maintenance free. For years composite decking manufacturers advertised their products as maintenance free. Eventually there were some class action lawsuits that followed once homeowners found that these products were not maintenance free.
The truth is there is no such thing as maintenance free especially outdoors. Even inside you do not have maintenance free kitchen floors so you should stop thinking maintenance free and realize that everything will require some maintenance.
On top of that some of these man-made composites have held up well and some have completely crumbled causing more class action lawsuits for these decking products. Many advancements have been made with the most recent products. The Florida sun is so harsh that we do not have a 10 or 20 year history with any of these products yet.
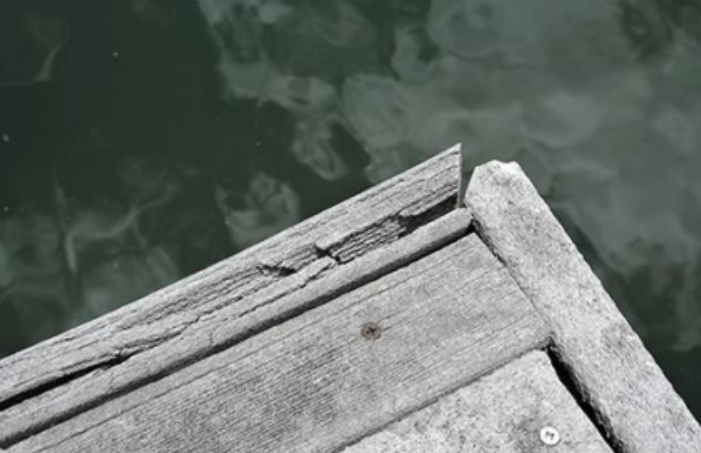
In the picture above the boat dock was built with composite decking material. It has mold growing on the surface, the surface has been wearing off and is badly pitting which leads to more mold growth. The outer skirting board is also badly deteriorating and crumbling.
Pros:
- Low Maintenance
- Made from recycled materials.
- Rot resistant.
- Most manufacturers offer 20+ year warranties.
Cons:
- Can be hot on bare feet.
- Many homeowners report that it’s very slippery when wet.
- Cannot be refinished.
- Expensive
If this is the option, you are choosing you should do some Google searches for reviews on the brand you are interested in. For example,” Brand Name decking complaints” and “Brand Name decking problems”. If you do your research on Google, you will often find if other homeowners have had a lot of issues with those products.
Exotic Hardwood Boat Dock Materials
There are many South American hardwood products that have proven to last 75+ years with very little maintenance. These species we recommend are Ipe, Cumaru, Tigerwood, Massaranduba and Garapa.
These hardwoods are sustainably harvested and are naturally resistant to rot, mold, mildew and wood boring insect. In addition, they do not deteriorate like softwoods so even after many years they are still safe to walk on barefoot. Also, the wood is not hot to walk on barefoot like most plastic decking materials. This makes them some of the best choices for boat dock materials.
If you plan to build your new boat dock with one of these hardwood species, you can save significantly by using short length boards.
Pros:
- Low Maintenance
- Made from sustainable wood.
- Rot resistant.
- Proven to last 75+ Years. Theme Parks and Government installations use it for this reason.
- Resistant to mold and mildew
- Does not get hot on bare feet like plastic materials.
- Can be refinished.
Cons:
- More expensive initial investment
- Requires annual oiling to maintain color and help protect wood.